Les réglementations stimulent le besoin d’une nouvelle exploration de la conception
Avec le besoin continu d’atteindre les normes réglementaires d’économie de carburant, la réduction des émissions de CO2 et les exigences de performance, il est sûr de dire que l’allègement est une priorité majeure pour l’industrie automobile. Mais ce n’est pas aussi simple que d’échanger un matériau.
L’allègement automobile est un exercice d’équilibrage pour déterminer les bons matériaux avancés, les méthodes de fabrication et la conception de la voiture et des composants individuels. En fin de compte, cela fait une différence. Selon l’Office de l’efficacité énergétique et des énergies renouvelables du département américain de l’énergie , «Une réduction de 10% du poids du véhicule peut entraîner une amélioration de 6% à 8% de l’économie de carburant … quart de la flotte américaine pourrait économiser plus de 5 milliards de gallons de carburant par an d’ici 2030. »
La conception générative gagne du terrain chez plusieurs constructeurs automobiles qui cherchent à alléger leurs composants rapidement et efficacement. Grâce à la conception générative, les ingénieurs peuvent explorer plus d’options en entrant des contraintes structurelles et en définissant des paramètres pour le matériau, la résistance et le poids. Simultanément, la conception générative évaluera les méthodes de fabrication pour chaque sortie, y compris additive, soustractive et moulée.
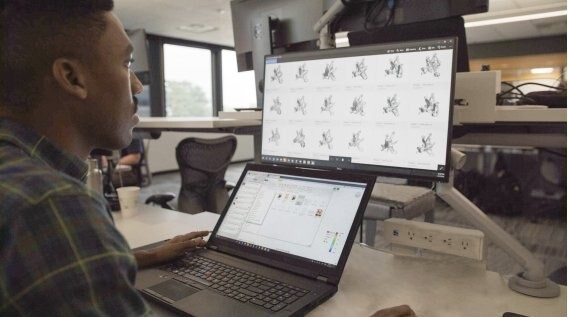
La technologie combinée à la puissance du cloud computing produit un éventail de solutions à explorer par un ingénieur, allant au-delà de ce qu’un humain seul pourrait accomplir dans le même laps de temps.
Continuez à lire pour découvrir comment trois constructeurs automobiles ouvrent une nouvelle voie et adoptent l’innovation pour alléger avec succès leurs conceptions.
#1: General Motors s’attache à un design génératif
General Motors s’engage à générer une valeur durable. Et l’entreprise fait un grand pas en avant dans la conception automobile pour imaginer un avenir de voitures plus légères et plus efficaces.
«La conception générative est un moyen pour nous d’explorer différentes solutions de conception pour les pièces et composants de nos véhicules en utilisant le cloud et l’intelligence artificielle pour combiner l’ingénieur et l’ordinateur», déclare Kevin Quinn, directeur de la conception et de la fabrication additives chez GM. «En les faisant travailler ensemble, nous pouvons proposer des solutions de conception de pièces qu’il serait impossible de générer avec l’ordinateur ou l’ingénieur travaillant seuls.»
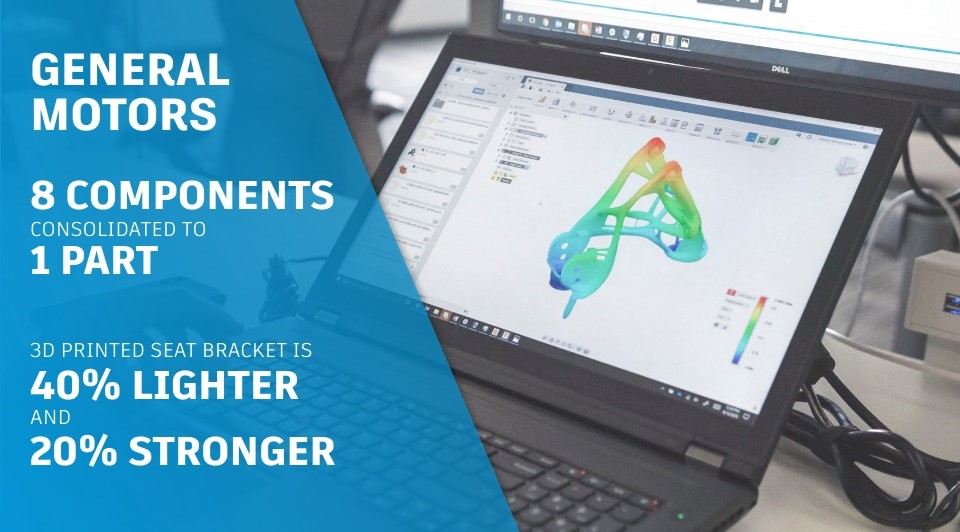
Dans un premier projet de validation de principe, les ingénieurs de GM et d’Autodesk ont appliqué la technologie de conception générative pour reconcevoir un petit mais important composant du véhicule – le support de siège où les ceintures de sécurité sont attachées. Le logiciel a produit plus de 150 options de conception valides basées sur des paramètres définis par les ingénieurs, tels que les points de connexion requis, la résistance et la masse.
L’équipe s’est concentrée sur un nouveau design, dont la structure organique qu’aucun humain n’aurait pu imaginer. Le nouveau support de siège est 40% plus léger et 20% plus résistant que la pièce d’origine, et il regroupe huit composants différents en une seule pièce imprimée en 3D, un autre avantage majeur de la conception générative.
GM prévoit d’utiliser la conception générative sur les futures conceptions de produits, et dans le cadre d’une alliance pluriannuelle axée sur l’innovation, GM et Autodesk collaboreront sur des projets impliquant la conception générative, la fabrication additive et la science des matériaux.
# 2: Honda R + D teste la conception générative d’un vilebrequin léger
Tout en recherchant une technologie de conception telle que l’optimisation de la topologie, la branche R&D de Honda au Japon a découvert la conception générative et s’est rendu compte qu’elle pouvait changer considérablement les normes de conception conventionnelles. Ils ont décidé de tester la conception générative avec un vilebrequin, une pièce de moteur qui nécessite une résistance et une durabilité extrêmes.
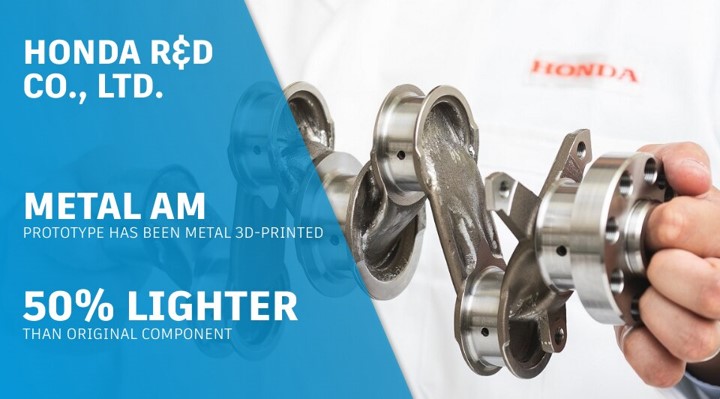
«Les vilebrequins doivent répondre à plusieurs critères fonctionnels», déclare Hirosumi Todaka, concepteur de machines mécaniques et fluides au laboratoire de technologie de pointe de Honda R & D. «Par exemple, sa forme doit pouvoir résister aux pressions de combustion et l’équilibre de rotation doit être maintenu. Ces facteurs ont dicté la forme du vilebrequin à ce jour. Au cours de la longue histoire du développement du moteur, la conception du vilebrequin était devenue une fatalité. Malgré cela, nous nous sommes fixé l’objectif ambitieux de concevoir un vilebrequin 30% plus léger que les modèles actuels. »
Le design génératif offrait ce que Todaka dit être «une configuration que je n’avais même pas envisagée en tant que designer». La nouvelle conception du vilebrequin a dépassé les objectifs avec une réduction de poids surprenante de 50%. L’équipe continue d’étudier le prototype et de rechercher d’autres applications de la conception générative pour d’autres pièces.
# 3: BAC crée l’une des roues les plus légères au monde avec un design génératif
La légèreté prend une toute nouvelle signification pour Briggs Automotive Company (BAC). La société basée à Liverpool conçoit et construit la BAC Mono, une voiture de course homologuée pour la route qui ne pèse qu’environ 570 kilogrammes. Afin d’accélérer et d’optimiser les performances, ils recherchent en permanence de nouvelles opportunités pour gagner du poids.
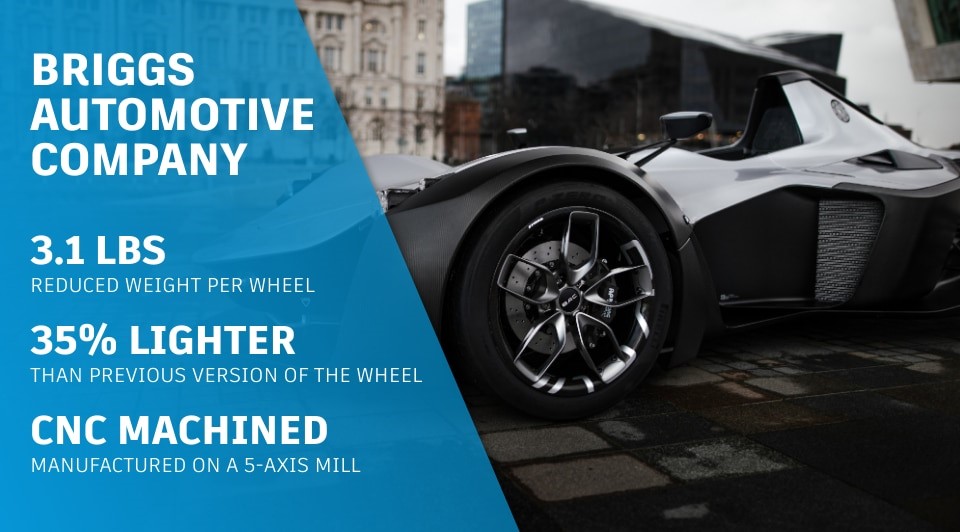
En utilisant une technologie de conception générative, BAC – littéralement – a réinventé la roue. Avec un poids de seulement 2,2 kilogrammes (4,8 livres), BAC a produit une roue qui était 35% plus légère que la version précédente et qui pouvait être fabriquée traditionnellement sur un moulin à 5 axes conventionnel. La nouvelle roue est non seulement plus légère, mais répond également aux exigences structurelles d’homologation et de certification en Europe.
«Nous avons 400 pièces sur la voiture qui sont usinées à partir d’aluminium massif sur une fraiseuse à 3 ou 5 axes», explique Ian Briggs, copropriétaire et répertoire de conception, Briggs Automotive Company. «N’importe lequel de ces composants pourrait entrer dans la conception générative et, pour probablement un coût très modeste, être réduit en poids. Nous les fraisons déjà, donc les fraiser un peu plus longtemps avec les conseils de conception générative serait le moment logique pour nous de commencer à économiser du poids. S’il y a une chance d’optimiser la conception, d’économiser du poids et de toujours le faire avec le même processus qu’auparavant, c’est un bon rapport qualité-prix et des économies de poids. Cela semble tout à fait pratique même aujourd’hui.