Imaginée pour la première fois à la fin de la Seconde Guerre mondiale, l’impression 3D a pris une place importante dans le monde industriel des années 1980. Puis dans les années 2010, elle était dans l’air du temps avec l’avènement de l’imprimante 3D peu coûteuse, censée bouleverser toute la relation entre conception et fabrication. Seul couac : les résultats étaient nuls !
La fabrication additive, ou impression 3D, a toujours été un excellent concept. Le secteur industriel a permis de la faire évoluer de façon adaptative, le potentiel à explorer est toutefois encore bien plus grand. Sans compter que la pratique de l’impression 3D grand public est à la traîne par rapport à d’autres technologies transformatrices de l’ère numérique telles que les réseaux sociaux, le commerce en ligne ou le cloud. Cet article présente les problèmes liés à l’impression 3D, en commençant par le procédé de fabrication par filaments fondus (FFF) destiné au grand public, qui utilise des matériaux plus robustes que les technologies SLA et DLP à base de résine. Nous examinerons ensuite l’utilisation industrielle de l’impression 3D, plus particulièrement son orientation vers la fabrication et la construction.
L’impression 3D FFF pour le grand public : problèmes et solutions
Une imprimante 3D grand public est essentiellement une grande pièce en mouvement. Mais le processus, qui consiste à appliquer un matériau sur un substrat pour créer un objet dans le monde physique à partir d’une conception numérique, implique un grand nombre de pièces plus petites et en mouvement elles aussi, qui peuvent toutes se désajuster. Des problèmes courants sont souvent la cause de la perte d’ajustement de ces pièces, et il est possible d’y remédier.
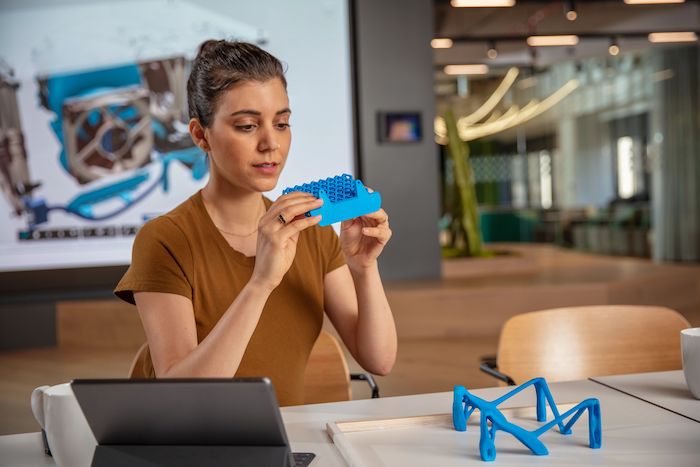
Problème n° 1 : des bourrelets
Lorsqu’une extrudeuse (la « tête » d’impression 3D) s’arrête ou change brusquement de trajectoire dans un virage serré, elle est soumise à la force d’inertie — qui affecte toute masse lorsqu’elle accélère ou décélère rapidement. Ce défaut peut amener l’extrudeuse à osciller légèrement d’avant en arrière pour se réorienter vers la position que lui impose le fichier source. Cela peut donner lieu à un motif ondulé caractéristique ou à des bourrelets à l’endroit du changement de direction.
1re solution : ralentir l’extrudeuse
Si vous rentrez dans votre garage en prenant le virage à 90 km/h, le souvenir sera beaucoup plus mémorable que si vous l’aviez pris à 25 km/h. Il en va de même pour la tête d’impression, et la solution est la même : ralentir. La plupart des appareils grand public disposent de commandes simples et accessibles via un menu sur l’appareil lui-même ou une application sur votre ordinateur ou smartphone. Vous y trouverez les paramètres permettant de régler la vitesse de l’extrudeuse. Aux endroits où le matériau est appliqué, il vous faut ralentir, mais là où il ne l’est pas, vous pouvez accélérer la cadence et gagner du temps.
2e solution : détecter une anomalie mécanique
Les bourrelets ou motifs sinueux erratiques ne viennent pas du logiciel ? Vous seriez surpris du nombre de fois où il ne s’agit que d’une vis mal fixée. La plus petite vibration causée par une attache qui se défait ou une fente minuscule dans une entretoise ou un support peut faire entrer votre extrudeuse dans des paroxysmes à peine perceptibles à l’œil nu. Observez attentivement votre imprimante en fonctionnement pour découvrir peut-être la vibration qui entraîne l’anomalie mécanique à l’origine du problème.
Problème n° 2 : la non-adhérence au plateau d’impression
Tout comme l’inertie excessive de la tête d’impression, l’inertie de la couche de matériau inférieure peut également faire des dégâts. Si la première couche n’est pas correctement fixée au plateau d’impression, toutes les couches suivantes seront déposées de manière légèrement décalée au fur et à mesure de son déplacement, la théorie du chaos faisant que le produit final ne ressemblera en rien à votre version numérique.
1re solution : niveler le plateau d’impression
Les imprimantes 3D grand public haut de gamme sont souvent équipées d’un plateau réglable doté de vis ou de boutons pour effectuer les ajustements. Assurez-vous que le plateau soit à niveau, un coin ou un côté peut être légèrement plus haut, de sorte que l’extrudeuse est plus éloignée de la table à certains endroits, ce qui laisse plus de place au matériau pour se tromper.
2e solution : contrôler la distance buse-plateau
Dans la plupart des cas, on peut régler la distance entre la buse de l’extrudeuse et le plateau (ou lit d’impression). Lorsque vous utilisez le matériau d’impression 3D le plus courant, soit le plastique polymère, il est judicieux de positionner la buse assez près du plateau pour permettre à une fine couche de filament de se déposer sur ce dernier et ainsi garantir une bonne adhérence. Vous pouvez trouver un juste milieu en fonction de la géométrie de votre pièce et du matériau. Sachant que chaque couche imprimée a généralement une épaisseur d’environ 0,2 mm, veillez à utiliser de très petits incréments pour trouver la distance idéale.
3e solution : ralentir la vitesse de dépose de la première couche
Si la première couche n’est pas réalisée avec suffisamment de soin, elle n’adhérera pas à la plate-forme de construction. Si elle se déplace et bouge, les couches suivantes seront décentrées. Modifiez vos paramètres pour déposer la première couche plus lentement que les autres, afin de laisser au matériau le temps de refroidir et de se fixer.
4e solution : ajuster le refroidissement
Là, on a (à nouveau) affaire à la physique. En refroidissant, le plastique rétrécit, et il se peut que la première couche adhère moins au plateau d’impression ou qu’elle se détache au fur et à mesure qu’elle se contracte. Tout au long de l’impression de votre pièce, le plateau est chauffé à une certaine température pour contrôler la vitesse de refroidissement. Ainsi, selon la complexité et les détails de votre modèle, la première couche de matériau peut se refroidir trop rapidement ou trop lentement. Les paramètres ou le micrologiciel de votre imprimante vous permettent d’adapter le refroidissement en fonction des caractéristiques de votre pièce.
Problème n° 3 : le cordage
Le cordage ou stringing se manifeste sous la forme de toiles d’araignées qui semblent recouvrir la voiture de course, la tête de Dark Vador ou le petit meuble imprimé en 3D, comme si le plastique continuait à s’écouler de l’extrudeuse alors qu’il aurait dû s’arrêter (ce problème est également connu sous le nom de suintement).
1re solution : régler les paramètres de rétraction
La buse de l’extrudeuse se retire du modèle lorsqu’elle reçoit l’ordre de ne pas ajouter de matériau. Ces spécifications dépendent à la fois des paramètres du logiciel ou du micrologiciel de votre appareil et de la complexité de votre modèle. Une buse qui ne se rétracte pas assez loin ou assez vite peut laisser s’échapper des fils caractéristiques qui s’accrochent ensuite à des surfaces où aucune impression n’est prévue.
2e solution : diminuer la température d’extrusion
Des paramètres de température du matériau trop élevés n’empêchent pas la buse de se rétracter au moment voulu. Néanmoins, le matériau qu’elle contient — désormais plus malléable à cause d’une température plus élevée — peut s’écouler en petites quantités, que l’extrudeuse tissera sur votre modèle lorsqu’elle se déplacera au point suivant.
3e solution : réduire les déplacements longs
Une extrudeuse qui n’a à effectuer que de courts déplacements entre les surfaces laisse moins de temps aux matériaux surchauffés pour s’échapper de la buse. Les mouvements plus longs favorisent le suintement. Les logiciels de construction intelligente peuvent apporter une solution à ce problème en planifiant la construction pour utiliser le plus petit nombre possible de longs déplacements dans un espace vide. Une autre solution consiste à modifier ou à programmer les réglages de l’extrudeuse afin qu’elle se déplace plus rapidement dans ces espaces vides. Avec moins de temps à disposition, le matériau est par conséquent moins susceptible de suinter lors de l’impression.
L’impression 3D industrielle peut changer le monde du BTP et de l’industrie
Imaginez un monde où les matériaux pourraient être appliqués là où on en a besoin, grâce aux technologies de fabrication additive. Le secteur du BTP pourrait utiliser l’impression 3D pour bouleverser le secteur industriel, à condition de bien faire les choses. Vous avez besoin de construire ou de fabriquer quelque chose ? Emportez une imprimante 3D et quelques blocs de matière première avec vous — du plastique à la limaille de fer ou au béton en passant par les structures organiques des organes — et imprimez votre structure, directement à l’endroit où elle va rester. Au lieu de partir d’un objet de grande taille et de retirer de la matière pour obtenir la pièce souhaitée, l’impression 3D utilise la quantité exacte de matière nécessaire, ni plus ni moins, ne générant ainsi qu’une faible quantité de déchets.
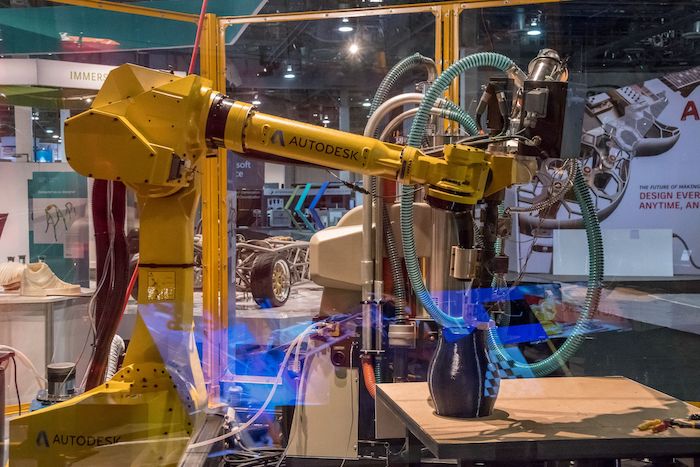
Le BTP fait partie des secteurs les moins durables au monde. En 2003, on estimait que 30 % des matériaux de construction livrés sur les chantiers étaient destinés à la décharge. De plus, la production mondiale de déchets issus de la construction devrait atteindre 2,2 milliards de tonnes d’ici 2025.
Ce chiffre ne tient même pas compte de l’utilisation de combustibles fossiles des véhicules et de l’équipement nécessaires à l’approvisionnement, au traitement et au transport des matériaux à destination et en provenance du chantier. À l’inverse, l’impression 3D effectuée directement sur le lieu d’intervention permettrait de réduire l’acheminement du béton ou du bois ou l’évacuation des déchets. Elle permettrait également de diminuer ou d’éliminer la quantité de déchets issus des processus de fabrication soustractive, qui doivent être éliminés ou réutilisés de manière raisonnable et sûre.
Sans compter que le matériel lourd et les méthodes de fabrication soustractive limitent également la construction aux zones accessibles aux poids lourds (ou aux vaisseaux spatiaux coûteux pour la mise en orbite d’instruments lourds). Les technologies additives permettent ainsi de construire dans des endroits plus reculés. C’est ce que suggère un projet de colonisation d’autres planètes qui consisterait à imprimer des structures en 3D à l’aide de matériaux provenant du lieu d’atterrissage du vaisseau spatial.
L’impression 3D pour la préproduction industrielle
Même si l’impression 3D ne va pas se généraliser dans le secteur industriel mondial avant un bon bout de temps, le procédé rend néanmoins déjà la préproduction moins chère, plus rapide et plus innovante.
Auparavant, pour développer des prototypes d’outils, de dispositifs ou de pièces, on avait besoin de pratiquement la même infrastructure de fabrication que pour la production, soit une usine entière de tours et de fraiseuses coûteux et encombrants.
L’impression 3D nous permet de faire évoluer les prototypes rapidement à partir d’endroits plus exigus, comme un studio de fabrication, un garage ou une table dans une chambre d’amis, en trouvant la conception optimale plus vite et à moindre coût en multipliant les itérations. Ce ne sont pas les propriétaires d’usines qui valent des milliards d’euros qui détiennent les clés de la fabrication : aujourd’hui, les géants de la technologie ont tous fait leurs débuts dans ces garages. Et il en va de même pour la révolution industrielle de demain.
En fait, c’est déjà le cas : l’impression 3D donne à la prochaine génération, celle qui innovera dans les façons de fabriquer, les outils nécessaires pour s’éloigner de la planche à dessin, développer et créer des prototypes meilleurs que ceux des producteurs industriels aux flux de travail bien établis. Du vite fait, bien fait. Telle est la devise.
Les limites de la technologie d’impression 3D
Malgré tout, le monde réel est bien loin de cette image utopique de fabricants que l’on croise dans la rue et qui vont sauver la planète du changement climatique et des déchets de chantier. Voici quelques-unes des limites qui pèsent encore sur l’impression 3D, tant dans le domaine de la consommation que dans celui de l’industrie.
Limite n° 1 : les matériaux
Les jouets de bureau et les presse-papiers en polymère ont beau être cools, ce ne sont pas eux qui allaient permettre à un tout nouveau procédé de se généraliser. Si presque tous les matériaux sont adaptés à la fabrication traditionnelle, seul un nombre limité de substances peuvent être fondues et passées dans une extrudeuse.
Malgré cela, on fabrique aujourd’hui les voitures, les ordinateurs portables et les téléviseurs à l’aide de processus bien établis qui permettent de maintenir le prix bas en répartissant le coût de fabrication sur un nombre quasi infini d’unités. Même si la fabrication par impression 3D était moins onéreuse (ce qui est faux), il faudrait alors constamment utiliser une technologie additive différente pour chaque matériau. Par exemple, pour construire une voiture contenant du métal, du caoutchouc, du plastique et du verre, vous aurez besoin d’un dispositif d’impression 3D différent pour chaque composant, en supposant que la technologie existe pour imprimer en 3D toutes ces substances (ce qui n’est pas le cas).
Limite n° 2: les coûts
1er élément de coût : l’équipement
Oui, il existe toute une catégorie d’imprimantes 3D en dessous de la barre magique des 999 euros, mais elles s’adressent au marché des jouets de bureau, et non à la fabrication. Unité par unité, l’impression 3D ne peut tout simplement pas encore se mesurer à la fabrication traditionnelle, et le type d’imprimantes 3D nécessaire à la réalisation de tout ce qui va au-delà du prototypage rapide à l’échelle industrielle coûte entre plusieurs milliers et plusieurs centaines de milliers d’euros, soit un équipement hors de portée des bricoleurs ou des amateurs.
2e élément de coût : les matériaux
Il y a une raison pour laquelle les services d’impression 3D sont plus onéreux que l’achat d’une imprimante 3D pour réaliser le travail soi-même, et c’est principalement les matériaux nécessaires. Le prix de ces matériaux diminue certainement au fur et à mesure que la technologie se popularise, mais les nombreuses méthodes soustractives établies utilisant des commandes numériques ou des tours permettent néanmoins une meilleure répartition du coût unitaire que la fabrication additive.
Les fabricants de l’industrie lourde peuvent se procurer des matières premières en quantité telle que le coût du matériau par pièce est presque négligeable. En revanche, le matériau d’impression 3D à base de polymère le plus courant, l’acide polylactique (PLA), coûte entre 20 et 70 euros le kilo, et le prix des variétés techniques plus spécialisées oscille entre 100 et 150 euros le kilo.
De plus, les résines de fabrication additive d’entrée de gamme peuvent coûter autour des 50 euros le kilo et peuvent atteindre 135 à 170 euros le litre. En d’autres termes, vous aurez dépassé de plusieurs ordres de grandeur l’investissement fait dans la fabrication traditionnelle d’ici à ce que votre volume de polymère vous revient meilleur marché.
Limite n° 3 : les connaissances
Le manque de connaissances en impression 3D est une arme à double tranchant. D’une part, en raison de la grande variété de formats propriétaires et de normes concurrentes entre les fichiers, les dispositifs et les systèmes d’exploitation, l’impression 3D n’est pas aussi simple que ses premiers partisans l’ont fait croire. Ses utilisateurs doivent également avoir une certaine connaissance des principes de la CAO, des autres systèmes de conception 3D et du fonctionnement du matériel.
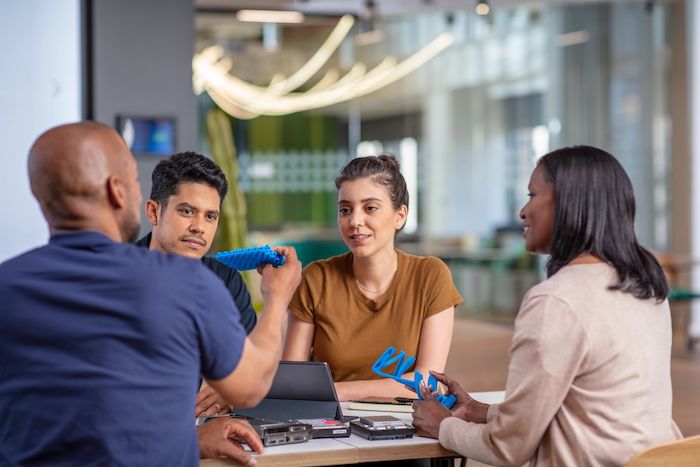
D’autre part, il est facile de s’accrocher à la technologie, de mettre la charrue avant les bœufs et passer à côté du but de l’impression 3D. On s’est servi de ce procédé pour fabriquer des bibelots, des pièces et des prototypes, mais le manque d’imagination est une entrave au développement de ce domaine. Quelle direction l’impression 3D prend-elle ? Quelles sont les limites de ce qu’elle peut réaliser ? Comment harmonisera-t-on l’utilisation des systèmes, des processus et des matériaux pour créer un monde meilleur ?
Même si à elle seule une pièce ne peut pas rivaliser avec un objet fabriqué de manière traditionnelle, ce n’est pas vraiment la question : la technologie additive peut servir à fabriquer un autre élément qui sera justement relié à cette pièce ou à ce prototype. En identifiant les liens au sein du système, vous pourriez découvrir de nombreux processus et pièces individuels capables de remplacer les méthodes traditionnelles, rendant ainsi l’économie plus intéressante. Ce sont justement les connaissances nécessaires à l’évolution de l’impression 3D.
Développer les entreprises grâce à la technologie d’impression 3D
Il est facile de se laisser emporter par les expressions à la mode et les tendances et de perdre de vue les atouts que nous présente l’impression 3D, mais les possibilités sont bel et bien là.
D’après Statista, le marché de la fabrication additive devrait connaître une croissance moyenne annuelle de 17 % jusqu’en 2023, et le marché des produits et services de fabrication additive triplera presque entre 2020 et 2026.
Plus récemment, le réseau financier du Moyen-Orient et de l’Afrique du Nord (MENAFN) a indiqué que le marché des filaments d’impression 3D (matière plastique brute) devrait connaître une croissance à un taux composé de 23,7 % jusqu’en 2025.
Tandis que le secteur de la consommation a connu l’engouement, la confusion et le désintérêt avant de finalement passer à autre chose, les fabricants, grands et petits, n’ont jamais cessé de repousser les limites, pour voir se réaliser l’utopie industrielle promise. Par ailleurs, des progrès ont été réalisés dans de nombreux domaines, dont notamment :
L’impression 3D composite
Compte tenu de la technologie d’impression et des matériaux disponibles, il est désormais possible de créer en une seule fois une pièce finie dont tous les composants sont intacts, même ceux fabriqués à partir de matériaux différents.
À partir d’une seule extrudeuse, imaginez-vous fabriquer un mur avec ses câbles ou ses conduits d’air déjà installés, ou encore un système d’engrenage et de courroie à partir de caoutchouc et de métal.
Les matières organiques
Des années se sont écoulées depuis que l’on a envisagé d’imprimer en 3D des organes compatibles avec les donneurs ; la technologie n’est pas encore tout à fait au point, mais les éléments de base sont en train d’être posés dans certains domaines insolites :
- En 2020, KFC, une entreprise qui n’est généralement pas associée à la haute technologie, a fait appel à un laboratoire russe d’impression 3D pour étudier une viande issue de la bio-ingénierie qui reproduirait le goût et la texture du poulet en vue de son utilisation dans les nuggets de poulet.
- Des scientifiques du MIT ont étudié la possibilité d’utiliser la cellulose végétale comme matériau de base pour l’impression 3D, plutôt que les plastiques à base de pétrole couramment utilisés.
- Et il existe déjà un matériau antiviral imprimé en 3D qui, selon ses inventeurs, serait efficace contre le COVID-19 sur les surfaces. Principalement destiné à l’utilisation dans les lieux publics, ce matériau sert à créer des produits tels que des protections de poignées de porte qui tueraient les virus et les bactéries.
L’avenir de l’impression 3D
Nombreux sont les secteurs technologiques qui ont connu de faux départs. Il est vrai que beaucoup de ceux qui se sont lancés dans l’impression 3D au moment de la montée en puissance du cycle d’adoption ont été désillusionnés et l’ont considérée comme une mode. Elle a mûri prématurément, si on peut dire. Les premières itérations ont été décevantes, mais au-delà des grandes promesses, de la poudre de perlimpinpin et des gros titres de la première génération, on réalise ce que les usines, les fabricants, les amateurs et les industries découvrent chaque jour : l’ère de l’impression 3D est enfin là.