Quand on pense à un labo, on a une image d’Épinal : des rangées de béchers et des machines qui ronronnent entourés de chercheurs en blouse blanche se déplaçant en milieu stérile, procédant à mille vérifications de leur travail. NEST (Next Evolution in Sustainable Building Technologies), situé sur le campus du Laboratoire fédéral d’essai des matériaux et de recherche à Zurich est loin de cette image : d’apparence, c’est une résidence futuriste, mais en fait il s’agit une plateforme de recherche et d’essai des pratiques du BTP et des matériaux.
« NEST est un labo qui a la tête à l’envers, explique Fabio Gramazio, architecte zurichois. Les expériences ont lieu à l’extérieur et la façade, qui donne son identité à la structure, est située à l’intérieur. »
Ce centre modulaire d’innovation et de recherche est intégré au campus du Laboratoire fédéral d’essai des matériaux et de recherche à Zurich. Dans ce NEST, de nouvelles unités de recherche, soit bureau, soit résidence, sont installés et remplacés en permanence. Ainsi le bâtiment, ou du moins sa façade, est-il en constant changement. Pendant ce temps, les fondations du bâtiment, dotées d’une cour intérieure, d’espaces partagés et d’un système prototype d’eau et d’électricité avancé, restent inchangées.
Mais un rapide coup d’œil aux sonnettes des appartements révèle la vraie nature du NEST. Il y a une vraie liste de noms, ceux des chercheurs qui habitent dans le bâtiment. « Ce qui rend la recherche si exceptionnelle ici, ce sont les conditions réelles, sans mesure d’isolement, insiste Reto Largo, directeur exécutif du NEST. »
Reto Largo est informaticien, et son père était entrepreneur dans le bâtiment, il est donc parfaitement à l’aise avec le BTP et le numérique, et très impliqué dans la coordination de la recherche liée à la réalité du secteur. NEST compte 160 partenaires, dont Autodesk Foundation et Autodesk Research. « Le risque financier pour les entreprises partenaires est inférieur au risque encouru lors de vrais essais dans l’économie réelle, explique-t-il. »

Russell Loveridge, directeur général des Pôles de recherche nationaux (PNR) Digital Fabrication, est également partisan de cette approche collaborative. « Si on veut relever les défis du futur numérique, on doit en finir avec les silos dans le BTP. La conception doit devenir interdisciplinaire et collaborative, une bonne fois pour toutes. »
C’est ce que le PNR Fabrication numérique, l’une des plus grandes initiatives pour l’innovation dans le bâtiment, espère voir sortir du NEST. La DFAB (abréviation de « digital fabrication ») HOUSE, unité résidentielle réunit plus de 30 partenaires et chercheurs impliqués dans huit départements à l’Institut fédéral suisse de technologie (ETH) à Zurich, dont des architectes, des spécialistes en robotique, des scientifiques des matériaux, des ingénieurs structure et des experts en développement durable.
La DFAB HOUSE, qui a ouvert ses portes début 2019, est le futur de l’habitat résidentiel. La planification ainsi que presque toute la construction ont fait appel au numérique. Les robots ont fabriqué les éléments en bois non standards, ensuite montés sur le chantier. Une imprimante 3D a produit le coffrage d’une élégante dalle de béton, qui servira de plafond du premier étage, et un robot mobile sur chantier a produit le treillis d’armature d’un mur en béton sans coffrage à double courbure.
Maintenant qu’elle est terminée, la DFAB HOUSE sert d’appartement aux chercheurs en visite et de laboratoire d’essai pour solutions d’habitat intelligent et technologies de l’Internet des Objets (IdO). Dans l’unité, tout est connecté en réseau, de l’éclairage à l’électroménager. Pour faire des économies d’énergie, la chaleur des eaux usées est récupérée directement des bacs de douches vers les échangeurs des radiateurs. Lorsqu’elle n’est pas utilisée, l’eau chaude retourne dans son ballon au lieu de refroidir dans les tuyaux. Ce processus élimine le besoin de garder l’eau à haute température, économise de l’énergie et empêche la croissance des bactéries.
La DFAB HOUSE est une des six unités installées dans le NEST. Il existe aussi l’unité de minage et recyclage urbain, conçue sous la direction de l’architecte Werner Sobek. Rien n’est collé ni enduit dans cette unité, ainsi les matériaux peuvent-ils être recyclés ou compostés dans le cycle des matériaux de cette construction. En suivant ce principe, l’équipe espère trouver de nouveaux moyens de préserver les précieuses et rares matières premières, tout en cherchant de nouvelles technologies d’assemblage.
En cours de construction actuellement, l’unité HiLo, prévue pour 2020, est un habitat basse consommation à hautes performances conçu pour démontrer le potentiel de la construction légère. Les rendus montrent une toiture qui reposera sur l’unité comme une toile suspendue, une coquille de béton autoportante sur sa courbe funiculaire. La structure du toit elle-même s’élève à un point et son épaisseur atteindra presque 3 cm en son faîte. Un étaiement efficient et innovant utilisant un réseau de câbles en acier tendus et une membrane textile constitueront le moule dans lequel verser le béton liquide. Le toit sera composé de trois couches : une couche extérieure faite de cellules photovoltaïques, une isolation intermédiaire et une couche de béton apparent.
« Nous étions innovants, même avec les éléments de la dalle du sol, comment Philippe Block, qui supervise le projet. La géométrie de la conception est telle que toute armature de renforcement est désuète, allégeant la dalle de 60 % par rapport aux dalles conventionnelles. »
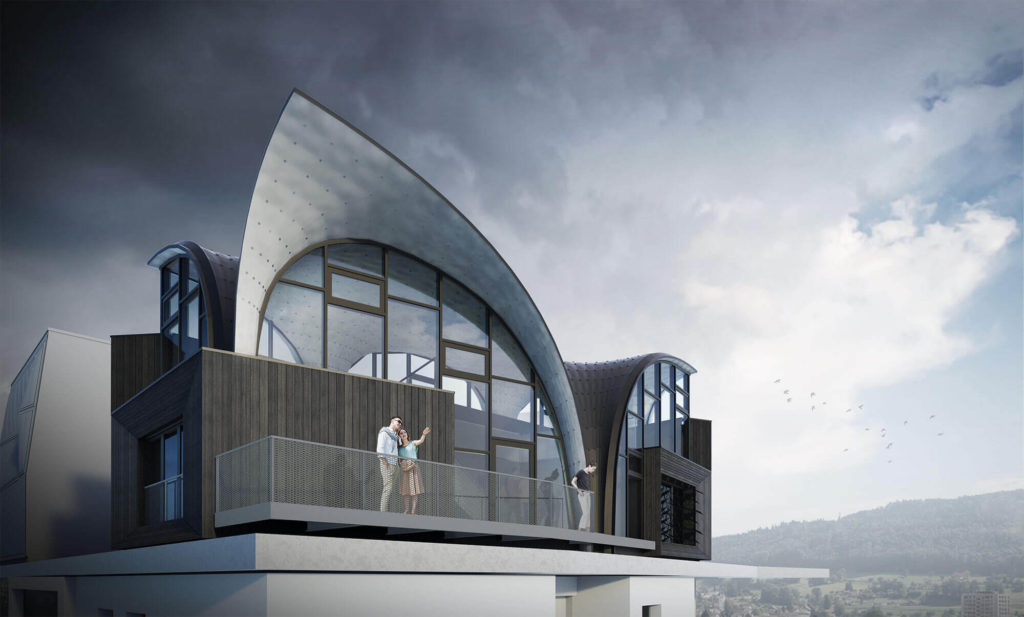
Une façade solaire adaptative avec modules solaires à placement automatique sera installée sur l’extérieur du HiLo. Les modules peuvent suivre le mouvement du soleil pour produire de l’énergie et fournir de l’ombre, ou s’ouvrir en se repliant hors de la façade au maximum de leur inclination. Chaque panneau est indépendant.
Cette façade est l’œuvre du professeur Arno Schlüter. Lors du développement des panneaux avec son équipe de recherche, le doctorant Prageeth Jayathissa a posé la question suivante : « Si l’environnement est en mouvement perpétuel, pourquoi l’architecture est-elle si statique ? » L’équipe s’est immédiatement lancée dans cette problématique, avec des logiciels soutenant une conception et une construction agiles et souples.
La maquette numérique de la façade solaire a été créée sous Autodesk Fusion 360, et le bâtiment NEST a été balayé au laser par l’entreprise suisse BIM Facility à l’aide d’Autodesk ReCap, créant des jumeaux numériques dans Autodesk Revit et BIM 360. Environ 3000 capteurs dans le bâtiment fournissent les données de gestion des installations comme la température et la qualité de l’air, qui sont transmises à la maquette Revit via la plateforme Autodesk Forge.
Ces données sont utilisées pour optimiser la gestion du bâtiment afin d’assurer un lancement fluide du NEST et une satisfaction totale des résidents à l’essai. Les instigateurs du projet espèrent qu’à l’avenir, les bâtiments et les technologies à l’œuvre seront plus pérennes dans nos pratiques, explique Gramazio Kohler. « Armé de suffisamment de souplesse et en acceptant l’inconnu au lieu de tout vouloir définir, il sera peut-être à nouveau possible de construire des bâtiments faits pour durer. »